HDPE Injection Molding
Durable, lightweight, and highly resistant to chemicals—HDPE injection molding delivers cost-effective solutions for high-performance plastic parts.
Home » Capabilities » HDPE Injection Molding
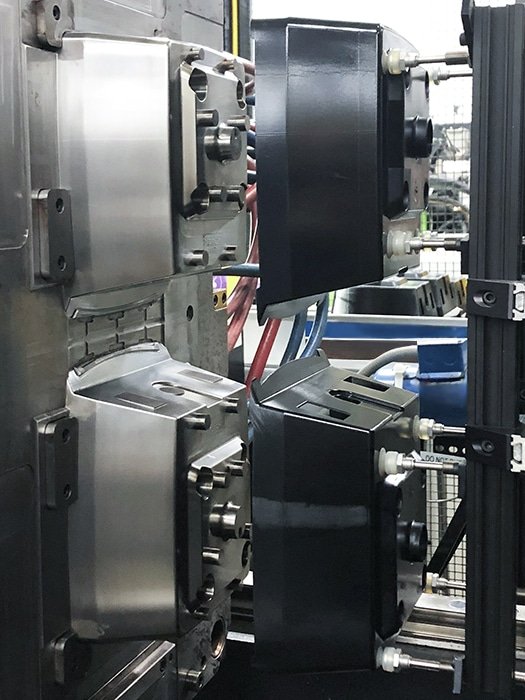
Erye Offer HDPE Injection Molding Service to Specific to Your Needs!
High-Density Polyethylene (HDPE) injection molding is a manufacturing process that produces durable, lightweight, and chemical-resistant plastic parts. Known for its excellent impact strength, moisture resistance, and flexibility, HDPE is widely used in applications requiring longevity and toughness. Its ability to withstand harsh environmental conditions makes it ideal for industrial, medical, and consumer products.
- Custom HDPE Part Manufacturing: Precision molding tailored to your specifications.
- Advanced Material Selection: Standard, UV-resistant, and high-impact HDPE options available.
- Tight Tolerance Molding: Ensuring consistent quality and dimensional accuracy.
- Multi-Cavity and High-Volume Production: Scalable solutions for cost-effective manufacturing.
- Secondary Operations: Including assembly, surface finishing, and custom packaging.
- Quality Control & Testing: Ensuring performance through rigorous inspection and testing.
What is HDPE Material?
High-Density Polyethylene (HDPE) is a thermoplastic polymer made from ethylene monomers through a low-pressure polymerization process. Compared to LDPE, HDPE has a more rigid structure, making it ideal for applications requiring toughness and structural integrity.
HDPE Molding Material Characteristics
- High strength-to-density ratio
- Excellent chemical resistance
- Low moisture absorption
- Good impact resistance
- High flexibility
- Good electrical insulation
- Easy to process
HDPE Injection Molding Design Guide
When designing HDPE injection molded products, it is essential to consider its unique material properties, such as its flexibility, shrinkage rate, and chemical resistance.
Item | Description |
---|---|
Wall Thickness Uniformity | Maintain consistent wall thickness (typically 1.0–3.5 mm) to prevent warping and uneven cooling. |
Shrinkage Compensation | HDPE has a high shrinkage rate (1.5–4.0%), so dimensional tolerances should be adjusted accordingly. |
Draft Angles | Use draft angles of at least 1–3° to facilitate easy part ejection from molds. |
Rib and Boss Design | Ribs should be 50–60% of the main wall thickness to avoid sink marks. Bosses should have generous fillets to reduce stress. |
Corner and Edge Radii | Avoid sharp corners; use a minimum radius of 0.5 times the wall thickness to prevent stress concentration. |
Texturing and Surface Finish | Consider HDPE’s relatively low surface energy when designing for paint adhesion or printing. |
Start HDPE Molding Project
Get high-quality HDPE injection molding parts! Contact with Erye to request a quote!
HDPE Injection Molding Application
Packaging
- Bottle caps and closures
- Food storage containers
- Chemical and detergent bottles
- Milk and juice jugs
Automotive
- Fuel tanks and caps
- Mudguards and splash guards
- Battery cases
- Interior trim components
Consumer Goods
- Toys and playground equipment
- Household storage bins
- Outdoor furniture
Agriculture
- Irrigation pipe fittings
- Seed trays and planting containers
- Livestock feeders